Welded Metal Windows vs. Mechanically-Fastened: What’s the Comparison?
A key feature of our Steel, Bronze or Alumin-Arte series of thermally broken metal windows and doors is that components are cut, welded, ground smooth, and then painted. This results in a different product than a mechanically-fastened system. Here’s a quick look at why we do welded metal windows, how we do it, and the results in terms of strength, aesthetics, and longevity.
Mechanically-Fastened Metal Windows
The standard method of assembling aluminum systems typically involves mechanically-fastened profiles, either nailed, screwed, or crimped together. It’s a quick and efficient way to manufacture, requiring fewer fabrication process steps.
Finishing costs are much lower with fastened systems. Profiles are painted in long linear lengths then cut and assembled. Finishing in linear lengths results in faster finishing times and improved transfer efficiency (material loss) than assembled frames.
Mechanical fastening is the industry’s standard method of assembling aluminum systems. Why would you want to seriously consider welded construction? The usual way of doing things can’t be too bad, right? Right, it’s not bad. But there are much better options.
Comparison: a Typical Mechanically Fastened Assembly System
VS. Dynamic’s Arte Welded Construction
- Typical mechanically fastened system with visible attachment seams & cut lines.
- Alumin-Arte cut, welded and ground system. No visible attachment lines for a ‘seamless’ look.
Why Welded Construction Matters: Strength, Aesthetics and Durability
Strength, aesthetics, cut lines and enhanced protection against corrosion.
Welded construction is extremely strong. For oversized frames, we’ll even add an additional aluminum or stainless-steel bracket (concealed) inside the glazing cavity to complement the strength of the welded joints.
Lines – there are none!
When profiles are mechanically-fastened, you’ll see the corner connections/mitre cut lines at every profile intersection. They are visible enough that they become, in effect, a part of “the look”. If the profiles do not align perfectly (keeping in mind that metal moves constantly under expansion and contraction) and depending on the color, shadow lines will occur or exposed shiny aluminum at the cut edges – particularly noticeable on dark finishes. With welded construction that is ground to a smooth finish, there are no exposed mitred cuts, the result is a clean, seamless finish – an aesthetic associated with steel windows.
Enhanced protection against corrosion.
When mechanically fastened, the mitre cuts expose the raw aluminum of the profiles. If mitred end cuts are not factory sealed with a liquid guard or similar sealer, the exposed aluminum can oxidize and creep under the paint, causing potential paint failure (peeling, flaking etc.). This is why mechanically fastened aluminum fabricators recommend edge guard protection if the project is within 3 miles of the ocean or some similar criteria. If the system is ordered without edge protection and is within a specified distance from the ocean there can be a warranty compliance conflict so it’s worth being sure. Read the fine print.
If you’re going to consider a mechanically-fastened system, ensure the supplier includes a protective coating at the mitre joints. In some cases, it can be a substantial cost increase as it adds an additional complexity to a normally expedited production system – a bit like stopping the printing press in full flow because someone wants one newspaper with the font in pink. The pink ink doesn’t cost much but the disruption to a volume-oriented production line is substantial.
With a welded system, by definition, there are no exposed mitre joints. This eliminates corrosion at the connections, thus there is no substantial cost increase to use a protective coating. You don’t need one.
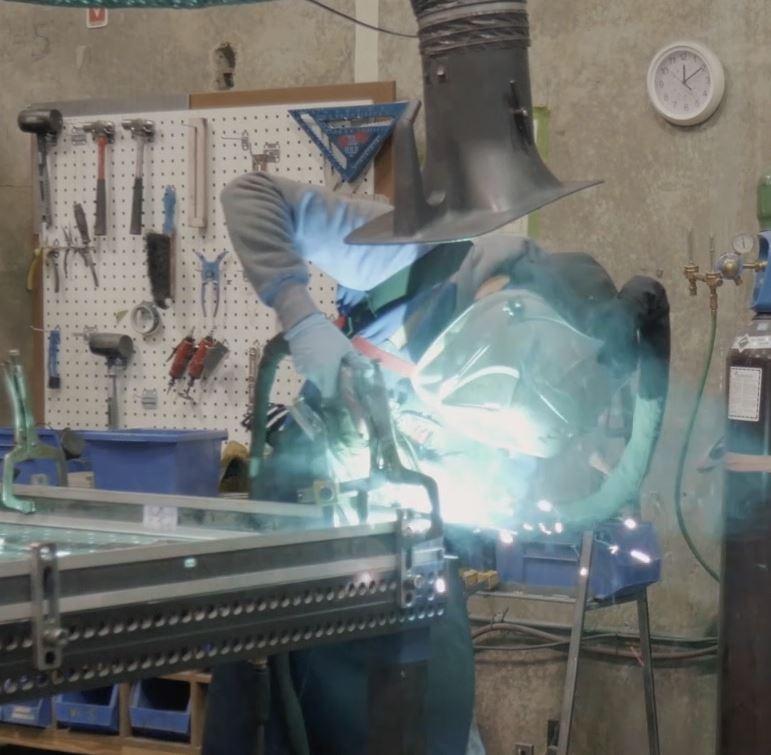
Cut profiles and weld together
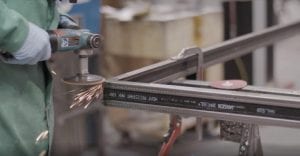
Grind welds to flush seamless surface
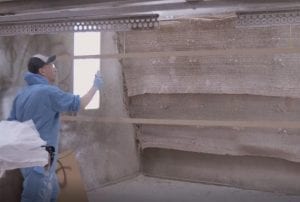
Units painted after assembly for complete coverage
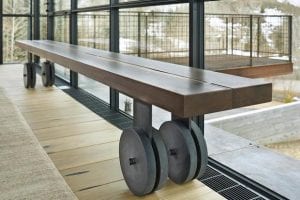
Result: Seamless joints with complete paint protection & coverage
Technical Benefits Summary
Welded construction systems will always cost more than a clip-together mechanically-fastened system. It’s the nature of the beast. There is all the added labor of detailed welding and grinding to get those surfaces seamless and perfect.
Welded frames are also painted once assembled. This costs substantially more than finishing the linear lengths used in mechanical systems as you’re finishing and moving large components, not bars of profiles. As an example, if a linear profile costs $20 to finish, an assembled frame will cost $100 to finish. You get what you pay for, but you do pay more.
Welded construction as a standard will have enhanced corrosion protection with no exposed mitred joints. Mechanically-fastened systems have exposed aluminum edges as a standard, and they can seal those edges at substantial cost to the project budget. Ensure you speak with your aluminum window supplier about sealing options and the resulting cost. The nature of welded construction means all joints are removed with complete paint coverage as a standard.
Architectural Aesthetics Summary
With a thermally broken narrow aluminum profile that is welded, ground smooth and then finished, you achieve an aesthetic on par with steel windows but at a lower price point than steel – which is the reason we designed the Alumin-Arte system in the first place. It is not intended to compete on price with a mechanically fastened aluminum system – it won’t. It is intended to offer a steel aesthetic when a) steel is over budget b) the project is ocean front and steel isn’t the appropriate material to specify (including stainless) and/or c) both of the above.
Welded construction is better. Better isn’t free. It’s just better.
Related Resources:
Dynamic’s Alumin-Arte and Bronze Arte Series
Learning Center: Performance Benefits of Thermally Broken Metal Windows
Learning Center: Are Thermally Broken Metal Windows Worth the Cost?